Feedback Devices
Feedback devices are a class of device required for closed loop operation. They provide a signal back to the drive or motion controller to monitor an operation or process and verify that proper operation occurs. In Motion Control applications, there are two primary feedback devices: Resolvers and Encoders.
A resolver is an electromagnetic feedback device which converts angular shaft position into analog signals. These signals can be processed in various ways, such as with an RDC (resolver-to-digital converter) to produce digital position information. There are two basic types of resolvers; transmitter and receiver. A transmitter-type is designed for rotor primary excitation and stator secondary outputs.
Position is determined by the ratio of the sine output amplitude to cosine output amplitude. A receiver-type is designed for stator primary excitations and rotor secondary output. Position is determined by the phase shift between the rotor output signal and one of the primary excitation signals.
The most popular type of Feedback Device is the Encoder. An encoder is an electromechanical device for translating linear or rotary displacement into a corresponding series of digital signals or analog output voltage.
Incremental Vs. Absolute Encoders:
Incremental Encoders
A device that generates electrical signals by means of a rotating disk that passes between a light source and photo detectors.
Incremental encoders have two output signals, or channels, commonly referred to as channel A and B. The A and B outputs are nominally 90º out of phase with each other and are interpreted by a motion controller to determine position/velocity information. The lead/lag relationship between the A and B channels provides directional information.
It is important to understand that each mechanical position is not uniquely defined. When the incremental encoder is powered on, the position of an incremental encoder is not known, since the output signals are not unique to any singular position. Incremental encoders often provide a third output that pulses once per revolution of the disk. This is typically called the Index, or Z-channel, and is commonly used for homing/reference moves.
Absolute Encoders
Absolute encoders have a unique value (voltage, binary count, etc.) for each mechanical position.
When an absolute encoder is powered on, the position is known. Absolute encoders most commonly provide digital data in a parallel or serial format to the motion controller which is used to determine position/velocity information.
Since they provide absolute position information when powered on they eliminate the need for a homing/reference move in a motion system.
Electromate supplies feedback devices for optical & miniature encoders throughout Canada in regions like Ontario, British Columbia, and Quebec.
Encoders, Inclinometers, and Tachometers We Provide:
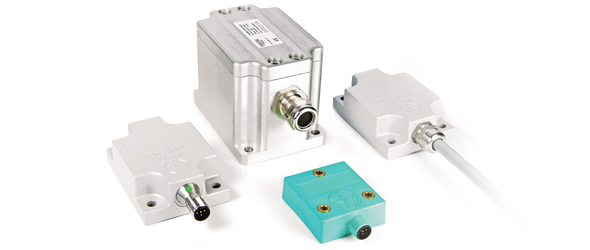
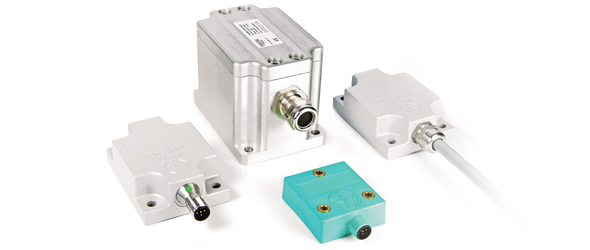
Inclinometers (Tilt Sensors)
Electromate proudly carries TILTIX Inclinometers made by Posital. Also called tilt sensors, they're designed to measure the angle of an object with respect to the force of gravity. These tilt or level meters determine pitch and/or roll angle and output these values via the appropriate electrical interface. Inclinometers are easy to integrate to an application, because there's no need for mechanical linkages aside from the installation itself. This is a real advantage for design engineers.
Draw Wire Encoders
Electromate offers POSITAL’s LINARIX draw wire sensors. They measure linear motion by displacing a stainless-steel wire wound around a wire drum. The drum actuates the rotary encoder coupled to it via a coupling. The wire in the housing is retracted by a spring. A proportional output is provided by the encoder. Measurements are accurate and reliable.
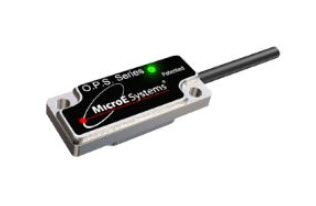
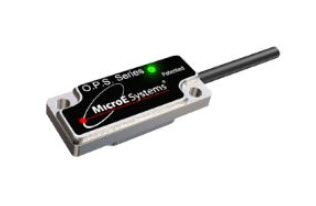
Linear Encoders
Linear encoders sense and digitize linear position change for position measurement and feedback to control systems. Linear encoders are available in two types, absolute and incremental, as defined by their position signals. Absolute linear encoders create a unique position signal that is available anywhere along travel. The exact position will be read after power cycling. Incremental linear encoders do not generate a unique signal. The encoder is zeroed after power-down and relies on another switch or encoder for initial reference.
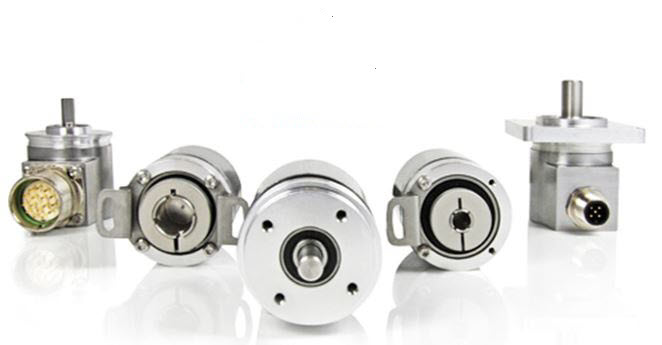
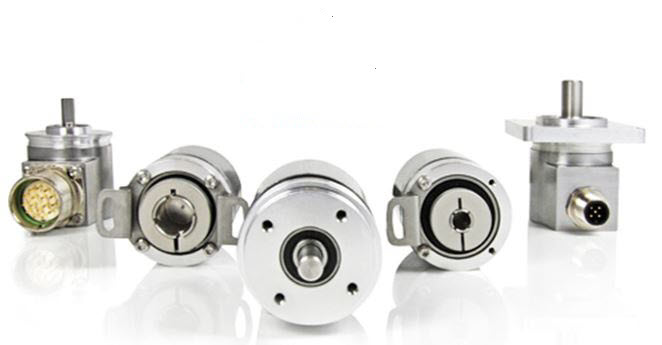
Rotary Encoders
Rotary encoders, also referred to as shaft encoders, are electromechanical devices that convert angular position or motion of a shaft to analog or digital output signals. Absolute encoders and battery backup incremental encoders provide precise and unambiguous measurements without losing track of their position due to a temporary loss of instrument power. Rotary encoders typically fall under one of three major mounting styles: hollow-shaft, hub-shaft, and shafted.
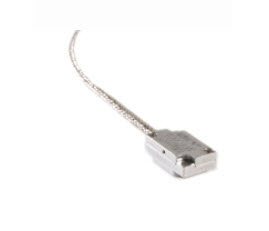
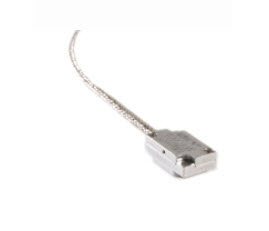
High Vacuum Encoders
High Vacuum Encoders from MicroE Systems are incremental encoders with small vacuum-rated sensors for motion control applications operated in a vacuum. Mercury™ and Mercury II™ vacuum encoders are specified in a wide range of applications due to their combination of performance, small size, and high vacuum rating. Choose from models with programmable digital output, analog output, or digital output right from the sensor, all constructed using vacuum-compatible materials rated up to 10-8torr. All sensors can be used with linear, rotary and arc segment scales.
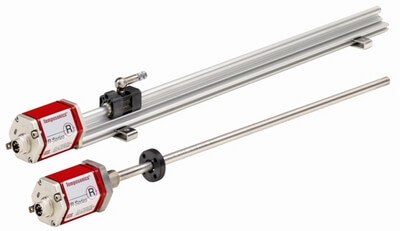
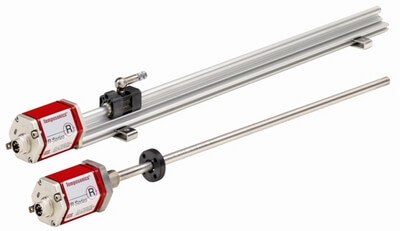
Linear Displacement Transducers
Linear displacement transducers are linear sensors that work on the magnetostrictive principle, whereby a torsional strain pulse is induced in a specially designed magnetostrictive waveguide by the momentary interaction of two magnetic fields. The interaction between these two magnetic fields (one from the moving magnet and one passing along the outside of the transducer) produces a strain pulse which travels at sonic speed along the sensor waveguide until the pulse is detected at the head of the transducer where the electronics are embedded.
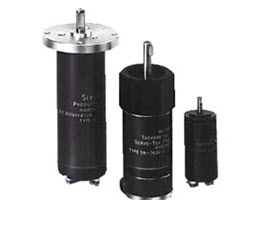
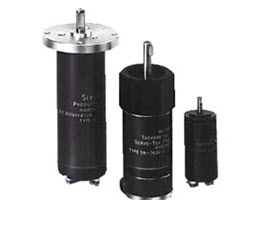
DC Tachometers
DC tachometer generators provide a convenient means of converting rotational speed into an isolated analog voltage signal suitable for remote monitoring and velocity control applications. Tachometers are particularly suited in precision integrator and velocity servo applications, both of which require a highly linear speed/voltage relationship with minimum ripple. The nearly pure dc output-with no phase shift-allows tachometers to be used as velocity feedback transducers for fast-response servos and other devices. Tach generators are also excellent rate generators for velocity damping in low speed position servo applications.